With close to 3500 spinning mills and a consolidated installed…
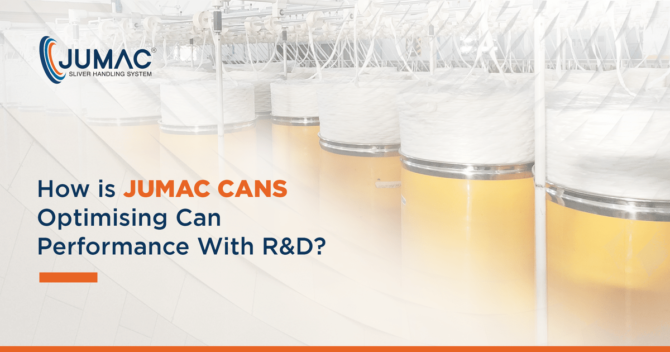
How is JUMAC CANS Optimising Can Performance With R&D?
The role of regular research and innovation in the field of textile machinery production is immense. Right from yarn quality improvements and removal of sliver imperfections to optimisation of the performance of HDPE spinning cans and caster wheels modification and ribbed bottom plate designing – practically all stages of sliver handling and yarn manufacturing can be improved through R&D and implementation of the latest technology. Jumac Cans, with its state-of-the-art production standards and dedicated in-house research team, is making a difference in this context. Over here, we will highlight how Jumac Cans ensures spinning can performance optimisation through rigorous research and study:
R&D Ensures Consistency and Standardisation Of Spinning Cans
The HDPE sliver cans manufactured by Jumac stand out in terms of their quality, stability and reliability. Continuous research plays a key role behind this. Top-class virgin HDPE (high-density polyethylene) sheets are used to design the cans, in order to ensure superior performance.
At Jumac, the in-house team is committed to manufacture and supply spinning cans with optimal sliver loading capacity and enhanced efficiency. These cans boost the overall productivity levels of spinning mills, and cut down on the total operational times as well.
Since its inception in 1974, Jumac Cans has steadily expanded its product portfolio – in its bid to deliver the best possible value to customers. At present, the company offers high-quality, customised sliver cans of different diameters (from 225 mm to 1200 mm) and other specifications.
R&D Ensures Greater Versatility & Applicability Of Spinning Cans
Top-notch versatility is one of the hallmarks of Jumac spinning cans. The company uses in-depth research studies to ensure that the sliver cans can be seamlessly used in different stages of spinning applications – from combing and carding, to draw framing, rotor tools and others.
The company has a state-of-the-art manufacturing facility, with the highly efficient material handling system ensuring the smooth production of cutting-edge spinning cans and other related accessories. The Jumac team controls, monitors and handles the production of its entire product range – leaving no scope for uncertainties.
The unwavering focus on continuous research and quality maintenance has helped Jumac consolidate its position as one of the top sliver can manufacturers in India. The company has clients across 18 different countries, and is a proud flagbearer of the ‘Make in India’ campaign.
R&D Ensures Ready Availability Of All Spinning Can Accessories
The operations at spinning mills hit a roadblock if and when spinning cans and associated spare parts & accessories are not available. The streamlined workflow and 360° business approach of Jumac ensures that its clients never have to face such problems.
Right from the tempered, rust-proof and heat-resistant spinning can springs (box/pantograph) and the top rims & bands, to the high-strength, fluff-free caster wheels (Jumac supplies both Nylon 6 and polypropylene varieties), colour cards, identification bands and others – everything is manufactured in adherence to the latest industry standards. The caster wheels modification and ribbed bottom plate design is done as per customer requirements. Product inventories are maintained – so that clients are able to find the ‘right’ spinning cans and accessories at the ‘right’ time.
Jumac Cans has always been a company that has embraced innovation and organisational transformations. Regular R&D is the pillar on which the company’s range of next-gen products – like the bump press cans, the perforated cans and the XL 1200 cans – are designed. With optimised can performance, piecings go down significantly and superior yarn quality is ensured.
R&D Ensures Minimal Sliver Imperfections
One of the biggest reasons behind the production of yarns of sub-optimal quality is the usage of inefficient spinning cans. Problems like sliver deflections, sliver breakage and sliver stretching are alarmingly common at many spinning mills – affecting productivity and operational efficiency.
The precision springs manufactured by Jumac keep the chances of sliver deflections and stretching at an arm’s length. Due research goes into the designing and customisation of highly stable spinning can components – so that the sliver quality is not affected in any way. Standardisation of sliver withdrawal is also done.
The Jumac team, through regular research and product improvement, also ensures quick and easy removal of accumulated dust and fluff from the HDPE sliver cans. Caster jamming is yet another issue that Jumac does away with – thanks to the non-abrasive and high-on-mobility caster wheels manufactured by the company.
R&D Ensures Superior Lifecycle Performance Of Spinning Cans
Through dedicated research and focused operations, Jumac has been successful in steadily elevating the quality of its products to match global standards. The company offers an optimal combination of manufacturing speed, scale of production, and professional expertise – to come up with best-in-class spinning cans for yarn-making.
The sliver cans manufactured by Jumac are of robust strength & durability, delivering excellent value-for-money to buyers. The cans (along with the other custom-fitted parts and accessories) are not affected by mechanical fatigue or other forms of wear & tear. The agile and process-driven operations of Jumac are a prime reason behind its success over the years.
Industry learning and tracking the latest scientific innovations from the fields of spinning can operations and yarn manufacturing form a major part of the R&D activities at Jumac. The company regularly participates in high-profile global events (SIMA Texfair 2019, ITMA Barcelona 2019, and more) – exhibiting its products and facilitating seamless knowledge transfer.
R&D Ensures Optimal Buyer Experience Through Mobile Technology
Optimised sourcing and usage of spinning cans go beyond just the quality of the products. The best spinning can manufacturers strive to provide a smooth end-to-end experience to buyers, through customer-centric operations and services.
With detailed R&D and market study, the Jumac team has come up with the cutting-edge and information-rich ‘Smart Can’ mobile app. The application comes with a host of user-friendly functionalities – like easy can ordering and tracking, access to accurate and updated technical information, detailed product knowledge and round-the-clock customer support.
The ‘Smart Can’ app also allows buyers to use unique QR codes to scan the spinning cans, and access real-time data (this is the ‘Scan the Can’ feature). We are in a ‘mobile-first world’, and everyone is looking out for information and services on the go. Through the powerful ‘Smart Can’ application, Jumac Cans fulfils this requirement.
R&D Ensures Availability Of The Best Sliver Cans At Highly Competitive Rates
The world-class production facilities of Jumac, together with implementation of the latest technologies and ongoing research, ensures top-notch productivity and optimised quality of the HDPE sliver cans. The cans rank high on the durability and longevity counts – and hence, deliver optimal value to buyers.
The efficient and streamlined manufacturing processes followed by Jumac make sure that the overall costs of production are managed carefully. This, in turn, empowers the company to supply quality-assured spinning cans to customers at competitive rates. The superior can performance pulls up the efficiency and product quality of the mills.
The team of researchers at Jumac also place due importance on the safety factor. There are practically no chances of slippage, overloading or other glitches – when the sliver cans are operating at high speeds. Varying volumes of slivers/fibres can be handled and processed by the cans, and all possible irregularities (e.g., yarn breakage) are done away with.
The global textile and yarn manufacturing industry is in a constant state of flux. The demand for quality-assured yarns is rising exponentially – and that, in turn, is bringing the importance of reliable spinning cans in focus. Jumac Cans has emerged as one of the best providers of spinning can solutions & optimised caster wheels modification and ribbed bottom plate design tools – through continuous in-depth research, usage of the latest technologies, and stringent quality control. The company has been scaling new heights, and it is set to drive the spinning can industry forward.
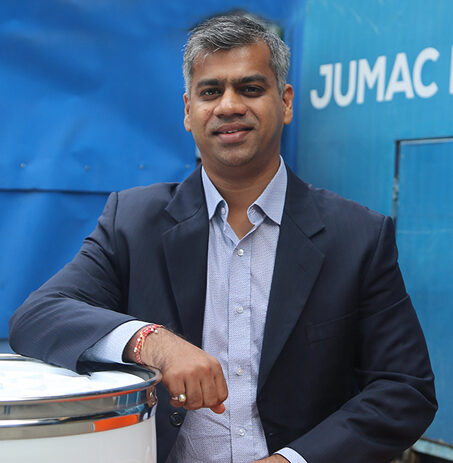
Passionate about transforming the industrial sector of textile and spinning industry with innovative solutions. Director at Jumac Manufacturing, leading spinning cans and accessories manufacturer and exporter from Kolkata, India.