The unwavering focus of Jumac on making textile spinning processes…
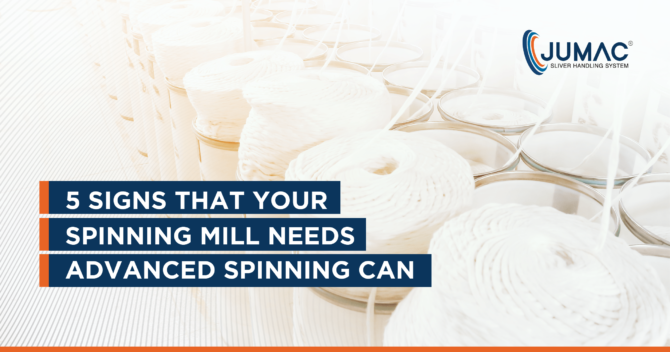
5 Signs That Your Spinning Mill Needs Advanced Spinning Can
With close to 3500 spinning mills and a consolidated installed capacity of nearly 850000 rotors, the Indian textile & yarn industry is comfortably one of the largest in the world. The market is highly competitive, buyers have a lot of options to choose from, and the demand for high-quality textiles is increasing exponentially. HDPE spinning cans, with their standardized quality, consistency and performance assurance, have emerged as one of the most vital cogs in the workflow of mills.
How would you know that your spinning mill needs a new & advanced spinning can? Look out for these indicators:
Productivity Is Low & Quality-Related Complaints Are Frequent
By the end of 2029, the size of the Indian textile industry is projected to touch $210 billion. With skyrocketing demand levels, you simply cannot afford to have sub-optimal turnaround times and poor overall productivity levels at your spinning mill. If the mill performance is not improving in spite of your best efforts, start looking for advanced HDPE cans that can give the requisite productivity boost.
The best HDPE sliver cans are manufactured with the help of the latest technology – ensuring superior performance and durability. Manufacturers typically have cutting-edge infrastructural facilities that enable constant monitoring and management of the spinning can manufacturing processes. Sliver cans of different diameters are available, to meet the varying needs of yarn manufacturers.
In addition, if you are bugged by disturbingly frequent quality glitches and defects in the yarns produced at your spinning mill – upgrading your sliver cans can prove to be effective. The top HDPE spinning can manufacturers customise their products to ensure that there are no inconsistencies and/or other problems in the slivers and yarns. When you deliver yarn of optimal quality, your customers are happy and your spinning mill continues to grow.
The Spinning Can & Accessories You Have Are Incompatible With The Machinery At Your Spinning Mill
If you are not careful while selecting sliver cans for your spinning mill, this negligence can come back to haunt you big-time. That’s precisely why it is of utmost importance to check the technical specifications of the spinning cans you are planning to buy. In case you are stuck with sliver cans that are not yielding the desired results, it’s time to look for more advanced alternatives.
Leading manufacturers and exporters of HDPE spinning cans, like Jumac Cans, typically ensure enhanced usability and compatibility with the latest textile mill machines. The sliver loading capacities of the cans are high – and they can facilitate agile & streamlined yarn production workflows. As a rule of thumb, select high-quality sliver cans that would add value at all the spinning stages (roving, carding, combing, etc.).
Make sure that the new sliver cans and accessories that you choose are indeed compatible with the existing machinery at your spinning mill. This will boost both the quality and the production speed of yarns, through improvements in operational efficiency. The best spinning cans are easy to maintain, have excellent longevity, and deliver optimal value for money.
Sliver Imperfections Are Becoming An Issue
When the yarn quality is uncertain, your business is going to suffer – there are no two ways about it. As the owner of a spinning mill, you must already be aware of the various imperfections and issues that can crop up during the spinning process – like sliver deflections, sliver stretching, fluff & dust accumulation, sliver breakage and more. In order to keep these at an arm’s length, using pre-tested & quality-assured HDPE sliver cans is of essence.
The top spinning can manufacturers offer the full range of sliver cans and related accessories that can effectively remove all common sliver imperfection problems. Make it a point to source cans with powerful springs (pantograph/box), caster wheels, draw frames, identification bands, top & bottom rims, bands, plates and other components. These will ensure easy mobility of the spinning cans, rule out chances of the loaded cans tipping over, excessive sliver stretching and breakages.
The draw frames, in particular, are extremely important for removing the accumulated fluff and dust that can undermine the spinning can operations in particular, and the quality of yarn produced by your mill in general. If required, you can also go for bump press cans or perforated cans to pull up your mill’s performance and efficiency.
Frequent Repairs & Replacements Posing A Problem
Purchasing spinning cans is an important investment for your spinning mill. If these cans have to be repaired and/or replaced frequently – that poses a big challenge, both from the cost as well as operational perspectives. Malfunctioning or damaged sliver cans can cause extended mill downtimes, resulting in losses.
If you have recently been forced to shell out big bucks on spinning can repairs – take the hint, and start looking for newer, better HDPE sliver cans. Always go for cans that are highly durable, do not undergo extensive wear & tear even after extended periods, and have robust mechanical strength. You should not have to worry about corrosion and abrasion-related issues either. A good spinning can bolsters spinning mill performance and lasts long.
In this context, it is also important to pay attention to the safety factor. That, in turn, brings to light the importance of sourcing sliver cans from a reputed spinning can manufacturer. These companies make sure that their sliver cans are properly tested, and do not cause any safety concerns – even when the machinery is operating at high speeds. There should be no risks to life or property whatsoever.
Lack Of Information Regarding The Quality Of Spinning Cans
The importance of HDPE spinning cans in optimising the yarn manufacturing process from the very start is immense. There is simply no room to be lackadaisical about the quality of the sliver cans that you use at your mill. Using sub-optimal spinning cans can hamper yarn quality and lead to other operational difficulties.
You should ideally look for sliver cans designed with top-class virgin HDPE sheets that ensure superior durability. Carefully check the quality of the caster wheels, precision springs, top/bottom covers, and the other components & accessories.
In order to improve the operations of your spinning mill, you should collaborate with a leading spinning can manufacturer that tracks and implements the latest innovative technologies to design high-performance sliver cans. Doing so will ensure fully uniform material handling, standardise all stages of yarn manufacturing, and take up the performance of your spinning mill to the next level.
At the end of the day, the onus is on your spinning mill to maintain a seamless balance of speed, quality and flexibility – to survive and thrive in the increasingly competitive markets. To ensure this, the ‘right’ HDPE spinning can has to be used at the ‘right’ time, and in the ‘right’ manner. Thanks to growing demands, robust investments and favourable governmental initiatives, the Indian textile & yarn industry is expanding fast – and with the help of carefully selected sliver cans, your mill can stay ahead of the competition.
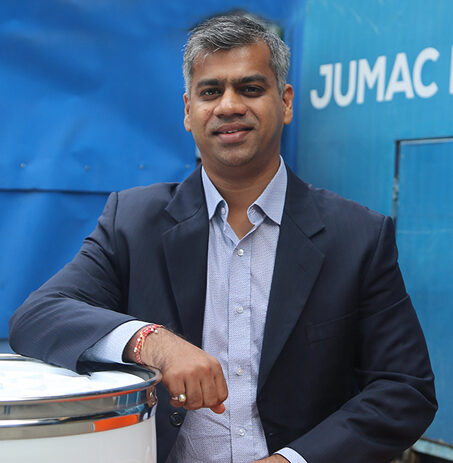
Passionate about transforming the industrial sector of textile and spinning industry with innovative solutions. Director at Jumac Manufacturing, leading spinning cans and accessories manufacturer and exporter from Kolkata, India.