Products of Jumac have high demand not only in India…
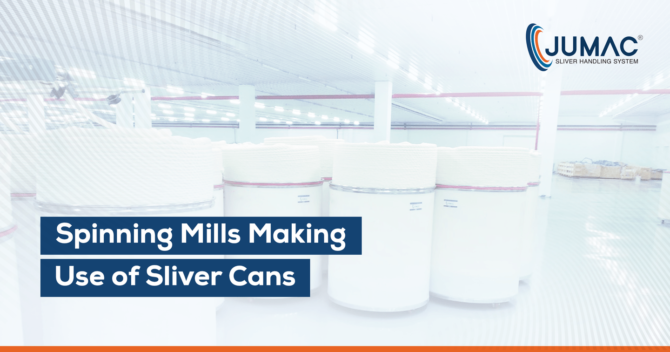
Spinning Mills Making Use of Sliver Cans
The Indian yarn & textile industry makes up nearly 25% of the annual worldwide trade in this sector. The country has one of the highest volumes of spindleage globally – and as demand volumes are increasing, the focus on yarn quality is also getting stronger. Quality-assured and custom-designed sliver cans are being used by all leading spinning mills – in order to rule out sliver imperfections, and maintain world-class yarn production standards. Let us here look at the importance of HDPE spinning cans for yarn manufacturing:
Preventing Snags & Ensuring Dimensional Accuracy
Most spinning mills have moved away from the rather difficult-to-use sliver cans made of composite materials, in favour of those manufactured with HDPE (high-density polyethylene) plastic. These HDPE spinning cans come with full recyclability. Environmental awareness is growing fast, and this is a big advantage in that regard.
The heat-welded material of the new-age sliver cans rule out chances of snagging and/or other defects during the filling and emptying processes. The dimensional accuracy of the cans is also very high. This ensures greater efficiency and minimal problems in spinning stages in particular, and yarn manufacturing in general.
Sliver cans are used by spinning mills in practically all stages of textile & yarn production – right from drawing and carding, to combing, roving, and other key phases. The workflow is made streamlined and safer, and unforeseen delays/downtimes are avoided.
Doing Away With Sliver Imperfection Risks
Leading spinning can manufacturing companies supply sliver cans with powerful, high-utility accessories. These include caster wheels, top & bottom rims, springs, vinyl & identification bands, and more. Since manufacturers have inventories of all the required fittings, spinning mills do not face any problem.
Inefficient sliver handling – often due to the use of defective spinning cans – can lead to a wide range of sliver irregularities. The custom fittings in the sliver cans ensure that these problems are easily avoided, and there is complete uniformity in yarn quality.
Apart from common issues like sliver stretching, deflections and breakage, spinning mills also need to be wary about dust/fluff accumulation. Good-quality spinning cans remove more than 70% of such accumulated dust. The caster wheels facilitate easy, smooth mobility of the cans. Risks of sliver imperfections become practically nil.
Enhanced Malleability & Energy Cost Optimisation
Superior tensile strength and high external impact resistance are hallmarks of the best sliver cans. Since the cans have excellent malleability, they can be easily folded/stretched/bent – without any loss of functionality. HDPE cans are corrosion-resistant as well, due to their negligible moisture absorption property.
Escalating energy costs are often a point of concern for spinning mills. By using quality-assured sliver cans, this problem can be effectively tackled. These HDPE cans can bring down overall energy expenses by ~5%, while optimising the sliver handling techniques, and lowering the total yarn processing costs.
To ensure yarn consistency and blend uniformity, there should not be any slippage or tilts during the yarn production. With sliver cans in place to maintain the correct positions, such risks are eliminated as well. As a result, the safety-factor of the workflow also gets a significant boost.
Availability Of Different Types Of Sliver Cans
The demand for sliver cans varies widely, based on the exact nature of the yarn manufacturing setup where they will be used. With that under consideration, spinning can manufacturers include different types of sliver cans in their portfolio – each with their respective advantages. Broadly speaking, buyers can choose from various types of rectangular & cylindrical cans.
The top suppliers invariably ensure uniform smoothness of the surface of the HDPE cans. Sliver migration and/or static are minimal – and the inner surface of the cans is typically scratch-resistant. The excellent durability of the sophisticated spinning cans spare spinning mills the trouble of having to worry about frequent repairs or changes.
By sourcing spinning cans from a reputed manufacturer, mills can also rest assured about the spring stiffness not deteriorating over time. Thanks to their quality, these sliver cans ensure superior material handling during transportation and storage. As a result, there are no risks of yarn quality loss.
Customisability and Scalability
Sliver cans can be used to process different sliver or fibre volumes, thanks to their easy scalability. Manufacturers supply cans with robust sliver loading capacities – and customised designs are available, to meet the exact yarn-making needs.
The finest HDPE spinning cans have top-notch safety features as well. This, in turn, makes sure that there would be no mishaps when the cans are being operated at high speeds. Industry-grade sliver cans are typically user-friendly, are easy to maintain, and do not always require the presence of human operators.
As yarn manufacturing becomes more agile and systematic with good sliver cans, chances of snaring, tangling, and/or any other irregularities are minimised. Spinning mills can also produce multi-layered yarns or threads without any hassles.
Enhanced Usability and Waste Reduction
Leading spinning can manufacturers work with a ‘customer-first’ philosophy – making it a point to ensure that their products are tailor-made to suit the needs of spinning mills. Compatibility with sophisticated spinning machinery (e.g., Trutzschler, Rieter, etc.) is a big advantage in this context. Mills do not have to face any delays while starting to use the sliver cans.
The excellent mechanical strength of virgin HDPE sheets make sure that the spinning cans are highly flexible, and are not affected by external stress. In particular, the joints are well taken care of – so that there is no yarn breakage.
At all stages of yarn manufacturing, considerable volumes of wastes are generated. As such, spinning mills have to give importance to their waste-management procedures. Sliver cans help in this as well. By bolstering the efficiency of workflows and minimising wastes, these cans help mills operate in a ‘green’ manner.
While there is no dearth of spinning can manufacturers, not all sliver cans are of the optimal quality. It is extremely important for spinning mills to select and use spinning cans that are ideally suited for their underlying yarn production operations. In the rapidly growing textile industry, yarn manufacturing processes have to be seamless, consistent and highly flexible – and high-quality sliver cans play a key role in delivering the required efficiency.
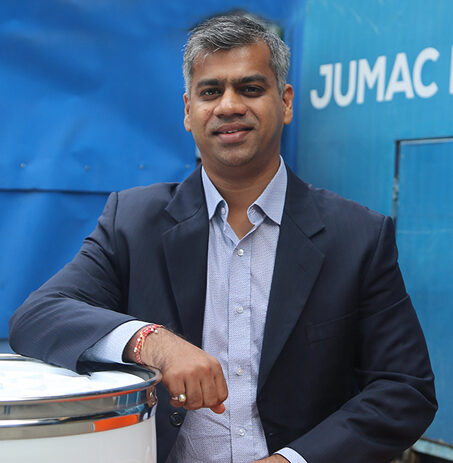
Passionate about transforming the industrial sector of textile and spinning industry with innovative solutions. Director at Jumac Manufacturing, leading spinning cans and accessories manufacturer and exporter from Kolkata, India.