The unwavering focus of Jumac on making textile spinning processes…
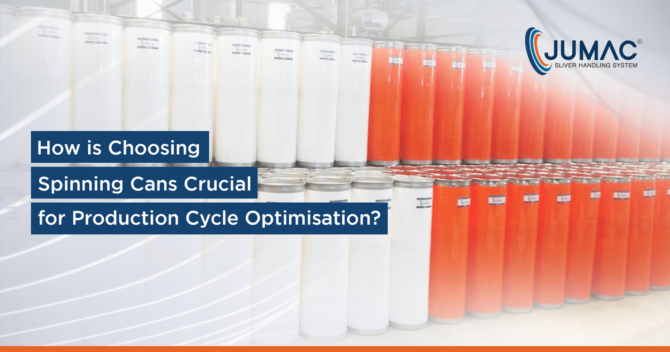
How is Choosing Spinning Cans Crucial for Production Cycle Optimisation?
For many spinning mills across the world, mechanical downtime causes significant wastage of productive time. To maintain productivity and quality of output, mills have to make sure that they source their manufacturing tools and machinery from a reliable manufacturer, so that their production cycle is not hampered in any way. In particular, usage of high-quality HDPE spinning cans plays a crucial role in ensuring that the manufacturing process is continuous – and the yarn quality is never compromised. In what follows, we will take a look at the importance of choosing the ‘right’ sliver cans for maintaining seamless yarn production cycles:
Using Spinning Cans Of The Correct Physical Specifications
Depending on the scale of operation and the volume of sliver to be handled, the demand for spinning cans can vary widely. Buyers can browse through cans of different diameters – from the small 225 mm models, to the high-capacity 1200 mm varieties. It is always a good idea to check the entire portfolio of a manufacturer company, before deciding whether or not to buy spinning cans from it.
While choosing sliver cans for their operations, spinning mills have to check the material of the products. The best spinning cans are made of tempered and hardened virgin HDPE sheets, ensuring superior longevity, enhanced performance and better safety assurance. As a result, the maintenance requirements remain low and there are no safety concerns.
Apart from the anti-static HDPE spinning cans, customers can also opt for other varieties of heavy-duty cans. The focus should always be on selecting and using quality-tested and high-performance spinning cans that would be the best fit for the underlying operations.
Choosing A Spinning Can Manufacturer With Full Range Of Accessories
The unavailability of high-quality spinning cans and other accessories in a timely manner is often a big factor behind the inefficient production cycles at spinning mills. That’s precisely why it is of utmost importance to select a sliver can manufacturer that offers the entire range of spinning cans and accessories. Customers should not have to work with multiple suppliers.
Buyers need to ensure that their selected spinning can supplier has the capability to supply caster wheels, springs, draw frames, identification bands and other relevant accessories – as and when required. The best can manufacturers make it a point to ensure that the accessories they design play important roles in removing sliver imperfections.
The chosen HDPE spinning cans should have the requisite sliver loading capacity, and deliver enhanced operational efficiency. The choice of caster wheels, in particular, has to be done in such a way that problems of caster jamming (resulting in diminished sliver mobility) do not crop up in future.
The Importance Of Innovation & Manufacturing Standards
Yarn-making standards and technologies are evolving constantly. The demand for fine, quality-optimised sliver cans is rising exponentially. To keep pace with this ever-growing market segment, it is important for spinning mills to work with spinning can-makers who are focused on continuous improvement.
For instance, Jumac Cans – one of the top manufacturers and exporters of HDPE spinning cans – has always positioned itself as an innovation-leader in the sliver handling industry. The customised spinning cans (perforated, bump press, etc.) designed by the company bear testimony to this.
It is also important to check the overall manufacturing facilities and standards of the different supplier companies. As a rule of thumb, mills should go for products manufactured by companies that ensure full control and monitoring – to identify and iron out quality issues (if any) from the products.
Proper Attention Has To Be Paid On Different Parameters Of Spinning Cans
There is no dearth of spinning can suppliers with an exhaustive range of products. However, not all companies can promise the same level of quality and/or product standardisation. Prior to ordering, it is absolutely vital to check the different parameters of the spinning cans – to ensure that they will deliver optimal performance.
Right from spring pre-tensions, processes & capabilities, can diameter and height, to the caster wheels, can type (round, rectangular, etc.) and other custom components – everything has to be chosen with due care. While operating with heavy loads and at high-speeds, there should not be any uncertainty over the stability of the spinning cans.
The onus is on spinning mills to select pre-tested sliver cans that are versatile and can be seamlessly used in the different operational phases of yarn manufacturing. Apart from minimising process time wastages, the selected spinning cans should also be able to pull up productivity levels significantly.
Checking The Mechanical Compatibility Of The Spinning Cans is Important
The spinning machines being used at modern-day mills are becoming increasingly sophisticated. Randomly choosing spinning cans is always risky – since the cans may not be compatible with the spinning machines and equipment. That, in turn, can lead to lengthy production downtimes – as mills hastily have to look for replacements.
To stay away from such problems, customers need to make sure that the sliver cans they buy are fully compatible with their existing mechanical setup. If required, the spinning can manufacturer company can provide guidance regarding this (along with pointers for proper maintenance of the cans).
Before arriving at a purchase decision, spinning mills need to understand how the performance and longevity of the spinning cans will be affected by mechanical stress and fatigue over extended periods. The can springs should also not lose their tightness over time.
The Right Spinning Cans Ensure Best-in-Class Sliver Handling
Problems like sliver deflections, breakage and extended stretching are frequently encountered by spinning mill operators. Most types of such sliver imperfections are irreversible – leading up to the production of sub-standard yarns. Hence, it is crucial to ensure that the sliver cans a mill chooses will prevent all possible risks of sliver imperfections.
To do this, spinning mills can easily jot down a list of the probable sliver handling risks and issues. While choosing spinning cans and accessories, the mills can inquire with the manufacturing company regarding how the latter’s products will rule out the possibilities of such sliver damages.
The top sliver can manufacturers typically offer comprehensive machine handling assurance that is at par with international standards. Products that are manufactured in compliance with the latest quality parameters invariably deliver the best value.
Considering The Cost Factor
In order to cut corners, decision-makers at spinning mills can make the folly of selecting cheap sliver cans that do not come with quality assurance. While the upfront costs of such sub-optimal cans are low – their glitches are likely to hamper production cycles, leading to serious operational problems.
In order to avoid such scenarios, buyers need to understand that price should never be the sole factor they should consider, while choosing HDPE spinning cans. Ideally, they should work with a supplier that can offer a seamless blend of quality, support and competitive pricing.
Leading spinning can manufacturers have the ability to effectively manage their cost of production – thanks to their streamlined workflows and agile production technologies. As a result, their clients can easily select the spinning can(s) and accessories that deliver optimal performance – without having to go beyond their budget.
The best spinning can manufacturers typically make sure that their products are of robust quality, are highly durable, do not undergo performance degradation over time, and do not have to be frequently replaced or repaired. As such, they help spinning mills maintain agile production cycles and optimal yarn quality levels. In the increasingly competitive textile & yarn industry, spinning mills simply cannot afford to work with sliver cans and/or other machinery of substandard quality. They need to source high-quality sliver cans from reputed manufacturers, in order to stay ahead of the game.
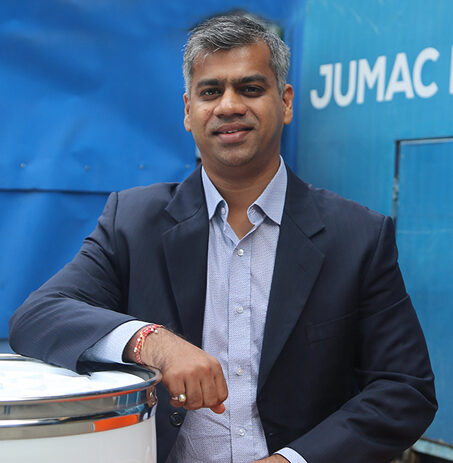
Passionate about transforming the industrial sector of textile and spinning industry with innovative solutions. Director at Jumac Manufacturing, leading spinning cans and accessories manufacturer and exporter from Kolkata, India.