Sliver is highly delicate. During high-speed spinning phases, apparently minor…
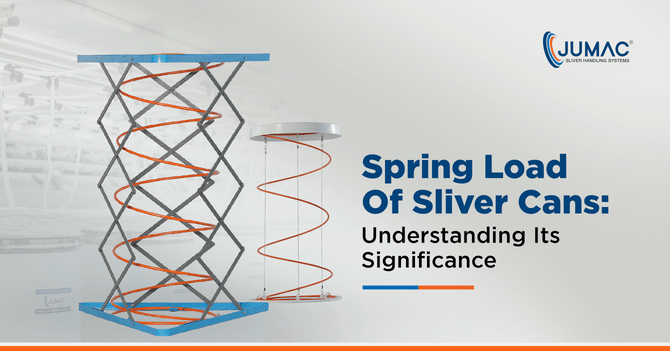
Spring Load Of Sliver Cans : Understanding Its Significance
Maintaining 100% yarn evenness is the prime objective of all spinning mills. However, there are several factors which – if not paid attention to – can lead to imperfections, causing the final yarn quality to be compromised. The importance of maintaining the ‘correct spring load‘ is paramount in this regard. Alternatively known as the ‘heart of spinning cans‘, the spring is instrumental in maintaining the distance between the feed roller and the sliver top level. Over here, we will highlight the key role that spring load plays in optimising the performance of sliver cans in particular, and textile spinning in general:
Understanding The Different Spring Types
Before getting into the role of spring load and the need to maintain it carefully, it is important to know about the two different types of springs used in spinning cans. These are:
Pantograph Springs
These springs are used in spinning cans with diameters ranging from 28” to 48”. The electro-welded and galvanised shutters make sure that the sliver height does not fluctuate at any time, and the uniformity of spring movements is maintained. Pantograph springs are tempered and hardened to ensure that key sliver parameters are not lost.
Must Read : How Does Pantograph Spring Ensure Better Performance Of Spinning Cans
Box-Type Springs
Made of strong high-carbon steel wires, box springs are carefully heat-treated, and come with complete rust-free assurance. To ensure sliver movement consistency, these springs are specially calibrated. In particular, box springs are highly useful in ensuring constant sliver height in the cans during rotor spinning as well as open-end spinning.
The Gap In Material Handling
During the yarn preparatory phases, the adverse effects of faulty material handling might not be evident. However, as the sliver moves on to the ring frame / draw frame, the problems become identifiable. Over the passage of time and extended usage, the spring-stiffness goes down – owing to the constant loading & unloading, intermittent / cyclic movements, and even excess humidity in the working environment. This, in turn, automatically affects the material handling standards, with the internal fibre cohesion levels going down and the yarn quality parameters getting hampered. As a result, a gap is created.
Note: At many mills, old sliver cans with poor spring stiffness levels are persisted with. Such ‘defective cans’ cannot adhere to the desired material handling standards.
The Correct Level of Can-Spring Pressure
When the spring load of the spinning cans is not checked with care, the internal fibre friction of the combed sliver is affected. As a result, the overall configuration of the fibre gets modified, there are falsified drafts, and sliver stretching / breakage can be a direct result. During sliver deposition and withdrawal, the role of the can-spring is vital – since the latter ensures that deformations do not go beyond the permissible level (given a certain load is applied).
Reports have shown that, for maintaining a smooth spinning flow with greater stability (while ruling out possibilities of imperfections), the ‘can-spring pressure’ level should be around 80% of the total capacity of spinning cans to store sliver. As this stiffness goes down after repeated usage due to fatigue loading – problems crop up, necessitating spring replacements.
The springs fitted in the spinning cans help in managing the sliver weight – so that there are no excess sliver stresses. The total tension in the can sliver should be a maximum of ~33% of the combed sliver strength. When the can itself is damaged / worn out and its spring load is not optimum, the lower stiffness results in higher-than-usual sliver stresses and resultant damages.
Unevenness (U%), Mean Count Irregularity (CV%) and Spring Load
In order to understand the level of yarn irregularities, certain actionable parameters have to be considered. Two metrics are used for this purpose. The unevenness in yarns is measured by U% (i.e., unevenness percentage), while the coefficient of mass variance is tracked through CV% (indicating the presence of irregularities). Let us quickly check how problems in spring load affects these two parameters:
At comparatively high storage times, there are risks of fibre leakage from the sliver coils. When the spring load is lower than what’s ideal, the unevenness – and hence, the U% goes up. Since the sliver is uneven, that results in yarn unevenness as well during the drafting phase over ring frame and speed frame.
When the can-spring stiffness goes down, the reduced spring load also causes the CV% to go up. Due to the extra compression of sliver height, the distance between the top layer of sliver and the coiler increases – and sliver stretching becomes a very real possibility.
Note: Lower spring load increases both the U% and the CV% of the bottom coils of sliver. The resultant sliver stretching happens at the creel zone.
Selecting the Right Spring Load for Spinning Cans
When it comes to selecting the ‘correct spring load’, there is no ‘one-size-fits-all’ solution. Several factors have to be considered, to decide the ideal spring load that a can requires. The factors include:
i) the height and width of the cans,
ii) the sliver weight per can,
iii) the type of fibre being used (e.g., natural fibre or man-made / blended fibres)
The ‘sliver hank’, which, in essence, is a packaged yarn type in coil form – also has to be factored in, while determining the proper spring load that a can requires for optimal stability and zero-tilt assurance.
Sliver Damages Due to Contact With Can Sides
Old, worn-out cans with reduced can-spring stiffness and deteriorated spring load cause greater non-uniformities in yarns. What’s more, in such spinning cans, the silver coils can easily come in contact with the sides of the storage cans (the spring load and stiffness is too weak to prevent this). As a result of this, sliver quality goes down further – both at the time of storage and processing.
How Can We Help?
At Jumac, it has always been our prime prerogative to enable our clients worldwide optimise operational efficiency levels on mill floors, and boost overall productivity levels. Proper sliver handling is essential for this – and ensuring the correct spring load in our cans is important.
In order to help our customers, we have a built-in ‘Spring Load Suggestion Calculator’. Once the different values have been fed into it (sliver length, sliver hank, process type, etc.), it automatically does the requisite calculation and displays the correct sliver weight and spring load values. Hence, uncertainties are eliminated – and probable glitches in sliver handling are done away with. Selecting the correct spring load paves the way for better spinning.
When the spring load is not correct, the overall yarn evenness is likely to be affected significantly. Over time, there is also the risk of the can-spring stiffness level going down – as a direct result of ‘fatigue loading’. The impact of incorrectly estimated spring load can become evident both during the sliver deposition and the sliver withdrawal stages. When not inspected and/or maintained regularly, the original sliver parameters get affected, resulting in yarn deformities. It also needs to be kept under consideration that when the quality of combed sliver is affected, the problems cannot be rectified at a later stage (e.g., ring frame, speed frame, etc.). By using precision-designed spinning cans and maintaining accurate spring load, mills can go a long way in ensuring optimal yarn quality from the very outset.
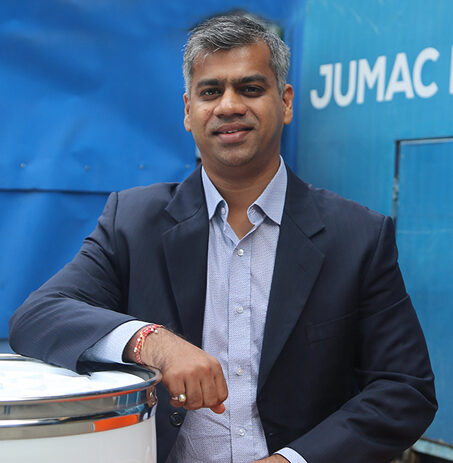
Passionate about transforming the industrial sector of textile and spinning industry with innovative solutions. Director at Jumac Manufacturing, leading spinning cans and accessories manufacturer and exporter from Kolkata, India.