Being recognised as a top exporter of spinning cans from…
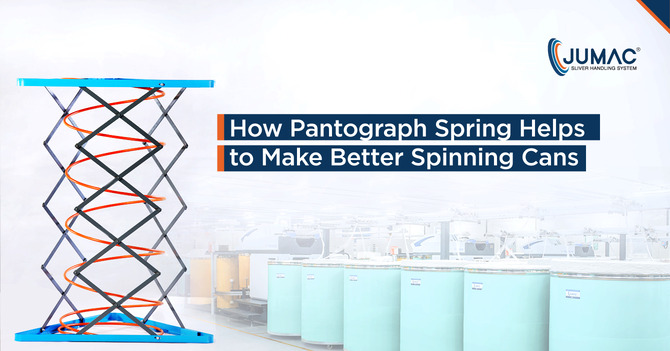
How Does Pantograph Spring Ensure Better Performance Of Spinning Cans
Sliver is highly delicate. During high-speed spinning phases, apparently minor tilting and/or displacements in the top plate of the sliver cans can lead to irreversible damages to the final yarn quality. To keep such problems at an arm’s length, the best spinning cans are fitted with highly-stable and resistant pantograph spring – that come with top-notch mechanical strength and uniform collapsibility. Thanks to the presence of these precision springs, sliver movements become a lot smoother, and chances of probable sliver deflections are minimised. Here’s a quick roundup of how pantograph springs help in boosting the usability and efficiency of spinning cans:
Enhances Sliver Loading Capacity
The tempered and precision-engineered pantograph springs have the capacity to wind and nest within the cans. This, in turn, increases the effective loading capacity of the cans in which they are fitted (when the spinning cans are almost full, this can be a major advantage). There are no risks of the can getting damaged when the pantograph spring is inserted and/or removed either. During high-speed spinning processes, these springs ensure that there is no tilting, and resultant sliver deflections, which can affect final yarn quality.
Offers Enhanced Performance Over A Long Time
HDPE spinning cans from the top sliver can manufacturers stand out in terms of their consistent performance, efficiency and longevity. High-quality accessories in general, and pantograph springs in particular, are a key factor behind this. These springs are systematically heat-treated to increase fatigue-resistance and overall durability levels. In addition, proper calibration is done in the pantographs – so that the requisite sliver volume/weight is supported at all times. The stability of the spring is yet another factor that boosts the operational efficiency of sliver cans.
Suitable For Different Types Of Fibres
At spinning mills, fibres of various types and qualities have to be spun. The pressure that needs to be exerted in the sliver cans depends on the precise nature of long-staple or short-staple fibre that has to be handled. Pantograph springs typically have excellent mechanical strength – and as such, they are ideal for supporting relatively high sliver loads. Of course, to get the best spinning performance and spinning can efficiency, buyers need to provide detailed information – like lid type & position, fibre type, sliver weight, can size & diameter, and more. The exact nature of pantograph spring required also varies with the spinning process (i.e., carding, combing, roving, etc.) where the sliver cans are being used.
Facilitates Uniformly Smooth Sliver Movements
During the different stages of textile spinning, different types of sliver imperfections can crop up. Apart from sliver deflections, there can be sliver stretching and consequent breakage, as well as excess sliver elongation. Leading manufacturers, like Jumac Cans, use pantograph spring in their sliver cans – to keep such problems at an arm’s length. Thanks to the triangular shape of the spring bottoms, the spring itself has uniform collapsibility, ensuring that risks of sliver stretching (due to sudden jerks) are minimised. When sliver movements are smooth, the original sliver parameters are retained – and final yarn quality is optimised.
Note: Other precision-engineered accessories also contribute to the overall usability of spinning cans. Dust-free and fluff-free caster wheels – that ensure smooth mobility – are a classic case in point.
Pantograph Spring Is Compatible With Spinning Cans Of All Sizes
Top sliver can suppliers have a diversified range of spinning cans in their portfolio (right from 225mm to 1200mm diameter). Pantograph springs come with full compatibility for the varying can sizes and diameters – so that there are no mechanical glitches or chances of sliver damage during operations. Apart from carded and combed sliver, the springs can also be used for efficiently handling synthetic sliver. Depending on the type of spinning can and the spinning phase, manufacturers fit the ‘right’ type of pantograph spring in the HDPE sliver cans.
Designed To Maintain Sliver Height Consistency
The crisscross design structure of the electro-welded pantograph springs is instrumental in supporting the required sliver height and gap. The shutters are manufactured with premium-grade mild steel (or, MS) – that is completely corrosion and rust-resistant – and ensures uniformly smooth movements of the spring (and, as a result, the sliver). The sliver balance is maintained by the galvanised covers (GP), that rule out possibilities of tilting. The usability of pantograph springs with plastic moulded covers of different diameters also warrants a special mention. The hardened springs make sure that sliver parameters are not hampered in any way.
Comes With Complete Quality Assurance
Given the importance of pantograph springs (and box-type springs, for that matter) in ensuring efficient sliver management and doing away with risks of yarn defects – their quality is of paramount importance. Springs sourced from reliable manufacturers offer great value on this count. There is very little mechanical fatigue even after extended usage, and the shape/tightness of the springs is not progressively lost over time. Through efficient spinning, it is possible to ensure yarn quality excellence from the very outset – and spinning cans with built-in pantograph springs play a vital role here.
Pantograph Spring vs Box Spring
Leading manufacturers like Jumac Cans offers a complete range of spinning cans and springs – box spring and pantograph spring. While both box springs and pantograph springs are commonly used in sliver cans, there are significant differences between the two. Unlike box springs, pantographs can be used in larger diameter cans as well (in addition to the smaller varieties). Also, the stability level obtained by coiling pantograph springs is significantly more than that delivered by box-type springs. Since the height between the lifting roller and the sliver coils at the top remains constant, there are practically no spring deflection/deformation risks. The sliver withdrawal process from the spinning cans also becomes smoother.
Extends The Service Life Of Spinning Cans
While most HDPE sliver cans are roughly similar in appearance, the ones that are fitted with high-quality pantograph springs stand out in terms of extended product life cycle. Springs bring greater consistency in spinning can performance, and minimise deviations that can damage sliver properties. The dimensional accuracy of pantographs further add to their advantages. Spinning mills should also, as a rule of thumb, go for sliver cans that are fully compatible with all the leading spinning machinery OEMs.
Springs in general, and pantograph spring in particular, are also known as the ‘heart of spinning cans’ – and for good reason. They make sure that there are no problems in handling laid-on sliver with enhanced load, diameter and other specifications. Consistency of sliver parameters is also ensured. Generally, a triangular bottom is used to support the pantograph springs, as well as boost the overall sliver loading capacity of the cans. The fact that these springs are available in the portfolio of sliver can manufacturers (along with other accessories) make things easier for spinning mills. Sliver handling calls for a lot of care and expertise – and pantograph springs are instrumental in making spinning cans more useful, reliable & efficient.
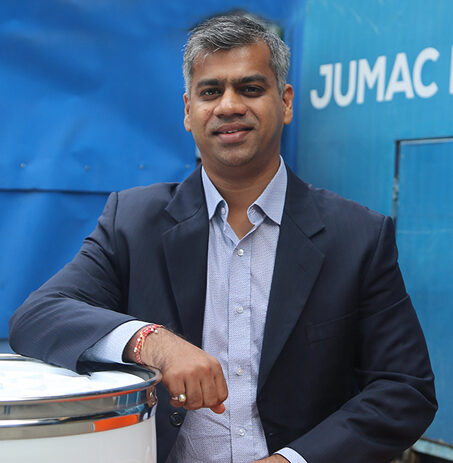
Passionate about transforming the industrial sector of textile and spinning industry with innovative solutions. Director at Jumac Manufacturing, leading spinning cans and accessories manufacturer and exporter from Kolkata, India.