With growing concerns over pollution and environmental integrity, the material…

Top 6 Challenges Faced By The Textile Industry In India
A CAGR of well above 15% clearly underlines the impressive rates of growth being registered by the Indian textile industry. According to recent projections, the value of textile exports from India is well on its way to meeting the $100 billion target, by the end of this decade. Leading spinning mills & spinning cans manufacturers are playing an important part in this, by constantly upgrading their operations, leveraging the latest technologies, and optimising their productivity levels.
However, amidst all the optimism and favourable trends (backed by timely governmental initiatives), there are certain points of concern – which can serve as roadblocks in the growth path of the textile sector. We will highlight these problems in what follows:
1. High Volume of Waste Material; Exposure to Chemical Hazards
More than 5% of the total volume of landfills worldwide are textile wastes. According to a recent survey, textile manufacturing was found to be the second-largest pollution-generator (after the oil industry). The growing demand for ‘fast fashion’ products is exacerbating this problem further. In particular, the Indian textile industry needs to be wary about the enormous amount of water wastage on a regular basis. Unless these resource wastages are minimised through carefully designed strategies, there can be long-term repercussions.
A wide range of ionic chemicals, acids, industrial enzymes, and alkaline solutions are used in the day-to-day operations of the textile industry. During the burning / singeing process (to remove floating fibres), different types of gases also get mixed in the ambient air. Many of these chemicals can pose serious health hazards (e.g., cancer risks). In order to keep such risks at bay, usage of proper protective gear is absolutely essential. The Indian textile industry is a source of employment for over 4.6 crore people – and their health cannot be compromised with.
Keep Reading: How to Manage Waste in Spinning Mills?
2. Paucity of Quality Raw Materials; Rising Costs, Supply Bottlenecks
In terms of cotton production, India has a unique problem. While our country contributes more than 25% of the total cotton production area in the world, the annual production is only around 8% of the global value. As a result, there is an unhealthy over-reliance for cotton imports from other countries (like Kenya, Egypt, USA, Peru, etc.). A spurt in pollution levels in many units across Europe, China and other countries, along with availability issues, has also resulted in raw material prices for the textile industry skyrocketing. This, in turn, is pulling up overall costs of production.
From dyestuff and acetic anhydride, to caustic soda and sodium bicarbonate – the prices of practically all textile industry raw materials are rising in the global markets (for some, there has been a 3X increase). In addition, there are various supply roadblocks as well – with logistics problems, and even unfavourable weather conditions playing a role. The unavailability of adequate, quality raw materials is forcing many manufacturers to miss out new orders, or fail to deliver existing ones.
Keep Reading: How Slashing The Import Duty On Cotton Is Likely To Affect Spinning Mills
3. Overdependence on Manual Effort; Infrastructure Problems; the Issues of An Unorganised Sector
The textile industry, both in India and abroad, has traditionally been a labour-intensive sector. However, Indian textile manufacturers are yet to pick up the pace – as far as technology advancements, particularly in terms of process automation & tracking, is concerned. The overdependence on manual labour is, hence, causing mistakes, oversights and random negligence, resulting in sub-optimal machine usage (Utilisation of Machines), frequent downtimes, and considerable loss of productivity. The top spinning mills in India are, thankfully, switching to a more automated process – to boost control, visibility, and ROI.
As a majorly unorganised sector (>90% of the weaving industry in India is unorganised), there are several infrastructure bottlenecks as well. In fact, research has shown that Indian textile mills lag behind many of their counterparts across Asia, in terms of infrastructure standards and production facilities. While the scenario is changing for the better, the rate of technology adoption is still painfully slow, causing problems.
4. Heavy Noise Pollution and Rising Environmental Concerns
The textile industry is a noisy one – there are no two ways about that. Daily operations, like machine gearing, air compression / suction, motion transmission, draw frame functioning and licker speeds, generate high amounts of unwanted (and often, loud) sounds. This is a serious point of concern for everyone working in textile mills – specifically when the sound pollution goes beyond the 1000 dB mark. Going forward, due attention needs to be given, to bring down the noise levels generated everyday at textile manufacturing units.
In a bid to maximise productivity levels and smoothen out the supply chain movements, environmental concerns often get relegated to the background by textile industry stakeholders. This can, and often does, lead to compliance issues with the existing environmental norms and regulations. Irreversible damages are caused to nature as well, as a direct result of the toxic wastes generated by the textile industry. The problems are mounting – and it’s high time for manufacturers to make sure that the impact of textile production (and any other ancillary activity) has minimal effect on the environmental integrity.
Note: While the Indian textile sector is growing steadily, there is regional unevenness in this growth. This is also something that needs to be gradually rectified.
5. Inadequate Attention Paid to Technology Upgradation and Regular R&D
For all the robust investments and government schemes to take the textile industry of India to the next level, technology adoption has somewhat taken a backseat (the TUF, or Technology Upgradation Fund, was launched way back in 1999). However, most of the scheme benefits have been accrued by the spinning sector – which is only one segment of the overall textile value chain – while other segments have lagged behind. The absence of systematic research activities, at least until recently, have also resulted in India perpetually playing the catch-up game in terms of leveraging textile technology (Textech).
The Indian textile sector can potentially gain big through the 100% automatic FDI (foreign direct investment) policy. However, in practicality, these benefits have not fully materialised – thanks to industry fragmentations, unorganised operations, and lack of economies of scale. The volume of annual FDI inflows need to grow exponentially, to sustain the development of this sector.
Keep Reading: How Is Technology and Innovation Helping The Indian Textile Industry?
6. Fragmentation and Skill Shortage are Affecting the Indian Textile Industry
While the average size of textile units (say, weaving units) in India is smaller than those in the US and China, the bigger problem is the acute fragmentation. Only around 5% of the apparel industry can come under the ‘organised’ classification – hurting the profitability of the fabric manufacturers in particular, and stakeholders in general.
The skill shortage in the Indian textile manufacturing landscape also warrants a mention. On average, 7 out of every 10 workers in this sector have very basic education (or are illiterate) – and hence, are unable to take their skillset forward, or help the sector grow beyond a certain point. The need of the hour is for encouraging education and knowledge transfer (through activities like vocational training programs, workshops & more). These will, over the long run, help in the expansion of the textile industry – both globally as well as in Indian rural areas.
Between 2017 and 2030, the Indian textile industry is expected to show a whopping 2X increase in productivity. What’s more, this sector also has the potential to generate as many as 34+ million new employment opportunities. The onus is on all the stakeholders in the textile sector value chain – right from the government to mill-owners & operators, spinning machinery OEMs and even top spinning can manufacturers to work in tandem and sort out the issues discussed above – making sure they do not derail the growth of the Indian textile industry.
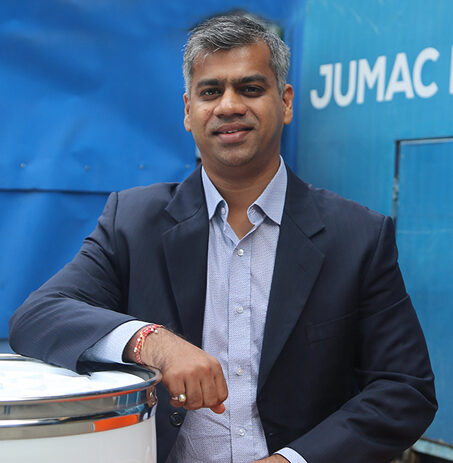
Passionate about transforming the industrial sector of textile and spinning industry with innovative solutions. Director at Jumac Manufacturing, leading spinning cans and accessories manufacturer and exporter from Kolkata, India.