With the world gradually recovering from the Covid-19 pandemic, the…
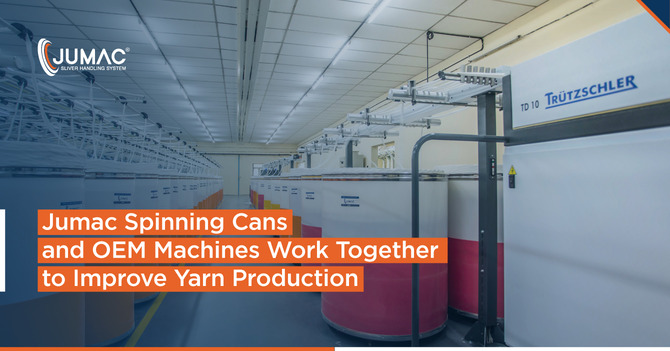
Jumac Spinning Cans and OEM Machines Work Together to Improve Yarn Production
In 2020, the value of the worldwide technical textile sector was just a shade under $165 billion. Cut to 2025, this figure is projected to zoom beyond the $220 billion mark – with the CAGR for this period hovering around 6.3%. With demand levels in the textile & apparels sector soaring (both in India and abroad), it is hardly surprising that spinning mills are increasingly focussing on the adoption of agile and seamless operating processes and operational technologies – to ramp up productivity levels and ensure the generation of premium-quality yarns. Spinning can manufacturer companies also have a key role to play in this context.
Mechanical glitches arising out of a lack of compatibility of sliver handling systems and the spinning machinery being used is – at many mills – a prime factor behind extended production downtimes, compromised sliver quality, and loss of productivity. That’s precisely why the HDPE spinning cans manufactured by Jumac Cans come with full compatibility assurance. Irrespective of the spinning machinery brand used at a particular textile mill, Jumac has things covered.
Which OEM Machines Are Jumac Spinning Cans Compatible With?
Rieter, Trutzschler, Marzoli, Saurer, LMW – the spinning cans designed by Jumac can be used in practically all the leading spinning OEM brands. Each OEM manufacturer offers separate machines for the different stages of spinning (e.g. carding machine, comber machine, etc.), and these quality-assured cans are compatible with all of them. As spinning technologies are evolving and smarter machines are being developed by mills – Jumac is evolving too, ensuring that OEM compatibility is never an issue.
Uninterrupted Production Cycles
When sets of spinning can are not compatible with the machinery already set up at a mill, that can lead to inordinate delays and production interruptions. Jumac cans do away with such risks. By sourcing these cans, mill operators can easily stop worrying over whether their spinning machines would support these cans or not. The assembly-line manufacturing process is maintained, sliver handling efficiency is maximised, and yarn production is significantly improved.
Compatibility With Carding Cans
The carding process has a direct impact on the quality and integrity of the final yarns. During this stage, the sliver strands are formed, impurities are removed, and neps are eliminated (to the maximum extent possible). However, if there are problems or technical mismatches in the spinning cans being used, problems can crop up.
As a knowledgeable, one-stop spinning can manufacturer, Jumac ensures that all its HDPE sliver cans have excellent loading capacities, offer superior stability, and protects all original sliver parameters. The compatibility with carding machines from different OEMs offers greater flexibility too – for mill-owners and operators.
Compatibility With Combing Machines
The combing process, which primarily gets rid of the short fibres that are not suitable for quality yarn production, can be affected when either the OEM machines or the comber cans do not function optimally. Once again, the OEM-compatibility of Jumac spinning cans proves to be handy during this stage. The comber noils (i.e. the short fibres) are removed by the spinning machinery – and the cans ensure that there are no accidental damages. Both the straightness and the length uniformity of fibres are maintained.
The customised, pre-checked spinning cans from Jumac add value to every stage of the combing cycle. Yarn hairiness is reduced significantly, and irregularities are removed as well.
Sliver Imperfections Arising From Mechanical Problems Are Minimised
There are many factors that can affect the yarn quality and spinning cans play a major role in the yarn making process. Forcibly using incompatible spinning can in the mill machinery can lead to a myriad of problems. The machines can get damaged – necessitating expensive repairs and/or replacements. The efficiency and longevity of the sliver cans also get affected. As a result, the overall quality of yarn production is likely to be affected. By investing on sliver cans with full OEM compatibility, the overall spinning process becomes a lot smoother and streamlined.
Given the delicate nature of sliver, a lot of attention has to be paid on their storage and transportation. When there is no dependency of the functionality of cans on the OEM machinery, yarn strength is maintained – and there are practically no chances of damage.
At this point, it is important to understand the types of sliver imperfections that can crop up as a direct result of inconsistencies between OEM machines and the spinning cans. Due to such problems, mills are often forced to tackle sliver stretching & breakage, sliver deflections and excessive stretching. These imperfections tend to become more pronounced during the high-speed spinning stages. When the spinning machinery and the cans work properly in tandem, chances of such sliver irregularities are kept at an arm’s length.
Quality Comes First
With competition levels in the textile and apparel sector rising exponentially, spinning mills have to – now more than ever – focus on the quality of yarns they produce. To help its worldwide clients in this regard, Jumac adheres to stringent quality parameters at every stage of its product manufacturing phases. Not surprisingly, the company – with its openness to innovation – has been able to cement its position as a premier spinning can manufacturer company in India.
High-quality virgin HDPE sheets, with robust resistance properties, are used in the spinning cans manufactured by Jumac. Cans of different sizes, diameters and other physical specifications are available – to meet the varying requirements of different OEM machines (and spinning stages). In order to maintain the required levels of stability, pantograph and/or box-type springs are used. This does away with tilting risks and other related problems.
Uneven sliver mobility can be a point of concern when the sliver is being transported from one machinery to another (i.e. from one spinning stage to the next one). This is handled by Jumac, by using dust and fluff-free casters in its spinning cans. Highly durable caster wheels – for both regular cans as well as trolley cans – are available. As such, sliver transportation on mill floors becomes smooth, efficient and risk-free.
Compatibility With Roving and Draw Frame Machines
The winding, twisting and attenuation functions that take place during the roving stage are facilitated by Jumac spinning cans with complete compatibility across machinery. The process of generating ‘low-twist lea’ from the fibres becomes more systematic – and chances of the sliver parameters getting affected are removed. The overall production costs are also maintained at manageable levels.
Draw frame refers to the spinning operation that is used for doubling, leveling and blending the sliver. Once again, the custom sliver cans from Jumac come in handy at this stage. The top players from the spinning machinery sector design specialised systems for the draw framing stage – and the company’s spinning cans are compatible with all of these systems.
Seamless Collaboration Of Jumac Spinning Cans And OEM Machines
For optimal productivity, mills need to ensure that all the spinning machinery has been set up, and is working properly. The importance of sourcing sliver cans from a reliable spinning can manufacturer is also paramount. The key lies in ensuring high on-floor operational efficiency levels, minimal system idle times, and enhanced productivity. This is possible only when mill operators do not have to worry about the compatibility factor.
More Convenience. Delivered.
The ‘customer-first’ business approach of Jumac has been a key factor behind its sustained success over decades. By ensuring that the usability and functionality of its cans are not affected in any way by the OEM machinery they are used in, the company delivers convenience and peace of mind to its customers. The need to look for machine-specific cans is done away with, and Jumac serves as an end-to-end sliver management solution provider.
The specialised spinning cans from Jumac – for carding, combing, draw frame, roving, open-end spinning & more – are approved by Trutzschler and Reiter projects, and they ensure minimal (if any) mechanical/operational problems. Since these cans are compatible with all leading OEM machines, risks of production downtimes and associated delays are also eliminated. With an eye on innovation and a vision to help mills modernise their on-floor processes, Jumac also ensures that all its sliver cans are supported by the proprietory Smart Can Technology. For the last five decades, Jumac has been constantly setting benchmarks in sliver handling excellence – and the OEM-agnostic spinning can products manufactured by the company are proven drivers of productivity & efficiency for mills across countries.
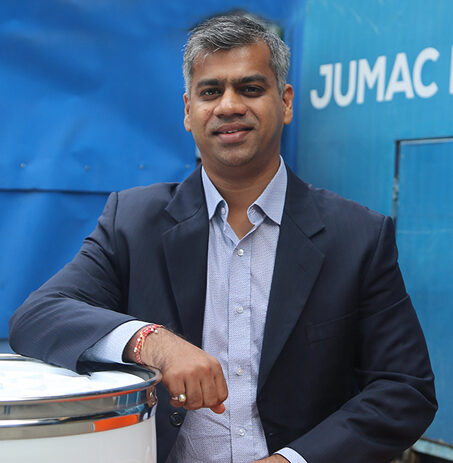
Passionate about transforming the industrial sector of textile and spinning industry with innovative solutions. Director at Jumac Manufacturing, leading spinning cans and accessories manufacturer and exporter from Kolkata, India.