Sliver cans are at the heart of yarn production in…
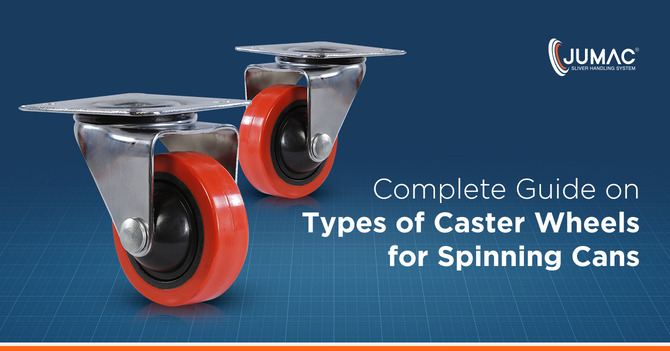
Complete Guide on Types of Caster Wheels for Spinning Cans
Selection and usage of high-quality sliver cans is integral for the production of fine yarns. Leading mills across the world are aware of this – and that’s precisely why the demand for customised HDPE spinning cans is rising exponentially. Given that the functionality assurance of these cans are derived from its components, buyers are increasingly looking for manufacturers that offer end-to-end sliver handling solutions. Due care has to be attached to the process of selecting spinning cans – and choosing the ‘right’ caster wheel is an extremely important condition.
Contrary to what many believed earlier, casters are much more than just wheels. Specialised caster wheels for spinning cans include the mount as well as the wheel itself – and they ensure smooth sliver transportation (and quality integrity) in the mill floors. Casters with different physical specifications (sizes, shapes, etc.) are available for the various types of sliver cans used in the spinning process. Here’s a comprehensive guide on the alternative caster wheel types that are used in spinning cans:
Caster Wheels In Terms Of Material
Different materials are used to manufacture customised caster wheels. The casters you select need to have the built-in capacity to meet the precise requirements. Some commonly used caster wheel materials are:
- Polypropylene – Caster wheels made with polypropylene are ergonomically designed, and have excellent resistance properties. As a result, they are popularly used in places that are exposed to moisture, chemical solvents and other potentially corrosive material.
- Nylon – Top-notch thermal stability is a hallmark of nylon (Nylon 6) caster wheel. In addition, the material can also work in harsh external conditions, and is not affected by solvents either.
Cast Iron/Ductile Iron
Casters designed with ductile iron or cast iron enhance the loading capacity of the object they are fitted with. They are temperature-resistant as well, offer smooth mobility, and are not likely to get broken or chipped frequently.
Polyurethane, rubber, stainless steel and neoprene are some other materials used in different types of caster wheels.
Note: Leading spinning cans manufacturers, like Jumac Cans, generally have both Nylon 6 and polypropylene casters (with zinc-coated bodies) in their portfolio.
Caster Wheels In Terms Of Load-Bearing Capacity
Caster wheels are also classified on the basis of their strength ratings, which indicates their load capacities. On this basis, casters can broadly be divided under three heads:
- Heavy-Duty Caster Wheels – These can generally support weights in excess of 140 kgs, without any significant mobility or mechanical problems. Extra-heavy-duty casters are also available.
- Medium-Duty Caster Wheels – Weights in the range between 70 kgs and 140 kgs can be mounted on medium-duty casters. Prior to actually putting on the load, it is always advisable to cross-check the caster capabilities with the manufacturer.
- Light-Duty Caster Wheels – As their name suggests, these casters come with the lowest load-bearing capacity (generally, under 70 kgs).
Note: For outdoor working environments and/or industrial set ups, buyers can also go for puncture-proof or pneumatic heavy-duty caster wheels. In general too, the nature and type of surface is a key factor in determining the caster option(s) to be selected.
Caster Wheels In Terms Of Maneuverability
The design of a caster wheel impacts its usability and maneuverability. From this perspective, there are two types of casters:
- Swivel Casters – The ‘kingpin’ (which, in essence, is a holding rivet/bolt) is considered to be the most important part of swivel casters. There is a cylindrical part of these casters, known as the ‘raceway’. The wheels can turn on the raceway – and the mobility is not limited to any particular direction.
- Rigid Casters – The caster wheels have limited maneuverability, compared to swivel casters. The fixed casters can only be rolled backward and forward – and as such, are not suitable for certain applications.
What is a Kingpinless Caster?
Given that the kingpin – when subjected to high mechanical stress – often develops glitches, the demand for ‘kingpinless caster wheels’ is gradually rising. These are specialised swivel casters with raceways, but without the holding rivet/bolt. While kingpinless casters are generally more expensive than ordinary swivel casters, their shock-absorption and stress-resistance capabilities are significantly higher.
In Terms Of Wheels Used
A specific type of caster wheel (that must be fluff and dust-free) are required for HDPE spinning cans. Similarly, other industrial casters require certain other wheel options. Caster wheels are available in the following types:
- Phenolic – These wheels are designed by systematic application of pressure and heat to glass/paper layers.
- Flanged – Since flanges are mounted on all the sides of these wheels, they can move on tracks – but, generally, not on bare floors.
- V-Groove – These tracks have very good traction, and they can be used with equal ease on both floor surfaces and tracks.
- Pneumatic – The high shock-absorption capability of pneumatic wheels is derived from the air filled in them. These wheels are available in both tubeless and tubed varieties.
In Terms Of Caster Wheel Hardness
There are several scales (e.g., the Brinell scale, the Shore D scale, the Shore A scale, etc.), to rate the degree of hardness of caster wheels. As a rule of thumb, metal casters are the hardest of them all – followed by the plastic casters, and finally, the rubber casters.
The hardness or softness of caster wheels directly influence their movements. Generally, the harder the wheel is, the lower is their ‘rolling resistance’. This, in turn, ensures that moving the casters at a uniform speed requires less force. On the other hand, the vibration emitted from caster movements is relatively lower when the wheels are softer. As a result, softer wheels can work more ‘quietly’ than their harder counterparts.
The width and diameter of caster wheels also need to be checked – particularly when they are being fitted to spinning cans for smoother sliver handling. Both the ‘starting resistance’ and ‘rolling resistance’ figures are inversely proportional with the wheel diameter and width. As such, moving the comparatively larger wheels is easy – and the load capacity is higher too. However, due attention needs to be paid to the stability factor as well.
In Terms Of Mount Types and Stem Types
Given the importance of caster mount on the overall functionality and durability of the product, a classification can be done on its basis as well. Stem mount, plate mount and bolt-hole mount (stemless variety) are the common types of mounts used.
The stem types differ across caster wheel models as well. Threaded, friction-ring, round, grip-neck, and square stem types are used. Other varieties, including customised options, can also be made available.
Note: Buyers also need to check the dimensions of the caster stem, or ask the manufacturer about the same.
Not all caster wheels have similar sets of features. There are spring-loaded casters that are ideal for usage in sliver cans. Braked casters can be selected as well, while hooded wheel models are available too. Casters can also be twin-wheeled in the housing. To buy caster wheels that meet industry expectations you need proper guidance.
Note: Depending on the underlying applications, the caster configuration varies as well (for both swivel casters and rigid casters).
The choice of caster wheel for sliver cans should ideally depend on the floor type at the spinning mills. Other key characteristics of the different types of casters – like bearings, hardness, operating temperature range, etc. – also need to be taken into account. Glitches in sliver mobility can lead to damages, and resultant sliver imperfections. As a result, the yarn quality gets compromised. By sourcing spinning wheels with the ‘correct casters’, mills can easily keep such potential risks at an arm’s length.
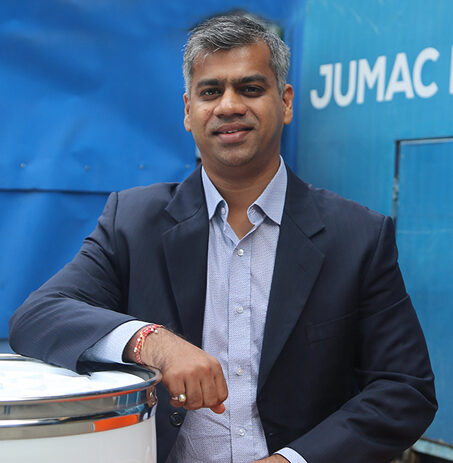
Passionate about transforming the industrial sector of textile and spinning industry with innovative solutions. Director at Jumac Manufacturing, leading spinning cans and accessories manufacturer and exporter from Kolkata, India.