Last month, the Union Budget for the 2022-2023 Financial Year…
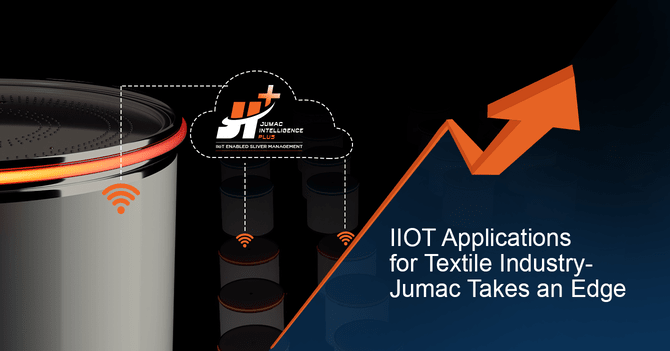
IIoT Applications for Textile Industry- Jumac Takes an Edge
Industry 4.0 is well and truly revolutionising operations in the textile and apparel industry. According to a recently published report, implementation of the latest Internet of Things (IoT) tools can improve mill productivity and time-to-market by up to 25%. As an industry-leading manufacturer & exporter of spinning cans, Jumac has identified this scope for innovation – and its potential to optimise can management and overall productivity. At the India ITME 2022 event held last month, the company announced its foray into the domain of IIoT (Industrial Internet of Things) – by unveiling the breakthrough range of Ji+ cans . Here’s a brief lowdown on how Jumac has taken an edge with its biggest spinning innovation so far – Project Ji+.
Paving The Way For Integrated Spinning Can Management
The Ji+ technology has been designed to operate as a real-time data-driven network. It will help in minimising sliver wastage, ensure that all spinning cans on the mill floors are optimally utilised, and productivity is maximised. Through live performance tracking, managing can performance becomes possible on the basis of actionable insights. The technology offers centralised control, bringing in greater visibility in the entire system. With Ji+, Jumac has used cutting-edge IIoT functionality to enhance spinning quality & efficiency.
Eliminates Risks Of Fibre Mix Ups and Errors
At various stages of yarn production, manual errors can happen. These errors (which may remain undetected) can affect the final yarn quality. The revolutionary Ji+ sliver management system keeps such problems at an arm’s length – by serving as a last-mile checking system that ensures foolproof results. The combination of proprietary software and a powerful hardware system delivers true value to mills.
Focused To Resolve Common Mill Problems
There are many instances of mill productivity being hampered due to yarn handling inefficiencies. Sub-optimal utilisation of sliver cans is often the reason behind this. In the absence of a reliable automated tool to track can utilisation, this problem cannot be satisfactorily resolved. In other words, ‘passive identification’ of spinning can operations cannot ensure the best results.
The Ji+ system looks to plug this gap, by ensuring can usage optimisation through continuous tracking and traceability. In particular, the enhanced visibility boosts the overall Utilisation of Machines (or, UOM). With the help of the real-time data generated, ‘can performance identification’ becomes more active. Since the LED identification bands are available in different colours, chances of traceability gaps (i.e., blind spots) are eliminated.
How Exactly Does Jumac Leverage IIoT?
While working on the Ji+ cans, the focus of the in-house Jumac team was constantly on implementing the very best of IoT services. For instance, these cans are powered by sensors that detect the sliver status inside the cans (i.e., tracks the sliver inventory in the spinning cans). This, in turn, ensures that mill operators do not have to check the sliver status manually, and there are no mistakes. All cans are used in an optimal manner, and inserted in the RIGHT MACHINES at the RIGHT TIME.
All the data generated by the Ji+ sliver management technology are shared and securely stored on the cloud. This is made possible with the help of the wifi-connected drivers in these specialised sliver cans. These drivers can ‘understand’ the sliver status (e.g., empty, almost empty, full). The data on the cloud are centrally accessible, and are viewable on a common dashboard.
Intelligence That Goes Beyond Can Tracking
At this point, it is important to understand that the IIoT-enabled Ji+ system is much more than just a tool to micromanage spinning can performance. The technology introduces smart automation that makes the entire can management workflow on the mill floors more ‘informed’ and efficient. It is ‘spinning intelligence’ at its finest.
Note: While the Ji+ technology can be implemented at any mill, it is particularly useful for the relatively larger spinning mills – where manual management of the hundreds of cans is an issue.
Visual Identification Made Easy
Monitoring the sliver status in individual spinning cans from a distance can be problematic. The Ji+ series of cans rule out all uncertainties regarding this. The cans have distinct identification bands (ID bands) in up to 12 different colours. This enables easier and quicker can status identification. Since the movement of sliver is tracked at all times and across machines, there are no chances of different yarns getting mixed up (thereby downgrading the sliver processing accuracy).
Since the can utilisation ratio is significantly improved by the IIoT-enabled Ji+ sliver handling system, the average ‘wait-time-per-machine’ goes down, and the overall ROI figure gets a big boost. Fault points, if any, can also be identified and resolved at an early stage (predictive maintenance). No delays, no production downtimes, no hassles.
Taking The Sliver Handling Ecosystem To The Next Level
To maintain its leadership position in the spinning cans manufacturing industry, Jumac constantly strives to make the sliver handling ecosystem progressively stronger. The announcement of IIoT-based spinning takes things forward in this regard. This particular innovation incorporates the essence of Industry 4.0 – with everything being traceable in a few button clicks.
Bringing Information To The Fingertips
For prompt resolution of service concerns, Jumac Cans leverages mobile technology – in the form of the Smart Can application. The Ji+ technology is fully compatible with the Smart Can system – enabling mill-owners and operators to access all can-related details on their devices (as well as on a centralised dashboard). The investment required is minimal enough, and connecting devices to the data cloud is pretty much straightforward as well.
The Final Word
Ji+ – the latest in the line of innovations by Jumac – is the result of dedicated R&D and brainstorming. The precise challenges and pain-points have been identified, to ensure that the solution indeed meets the exact requirements. With the help of ‘intelligent insights’ powered by Artificial Intelligence (AI), Ji+ goes a long way in bolstering time-efficiency, ensuring smarter spinning operations, and doing away with probable manufacturing errors.
The spinning industry has traditionally been a labour-intensive one. With the IIoT-powered Ji+ technology, Jumac has taken a bold step forward – to help mills leverage smart automation, and use data-backed insights to make their on-floor operations (particular focus on sliver can usage) smarter. Chances of manual errors, leading to yarn quality & accuracy degradation, will also be eliminated with these sliver cans. The growing global recognition of Jumac stems from its stance as an innovation-leader in the field of sliver handling – and with the latest IIoT application, the company has taken things to the next level.
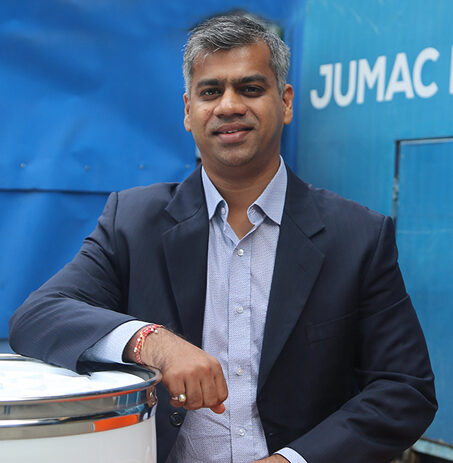
Passionate about transforming the industrial sector of textile and spinning industry with innovative solutions. Director at Jumac Manufacturing, leading spinning cans and accessories manufacturer and exporter from Kolkata, India.