Over five decades of our journey, we have mastered spinning…
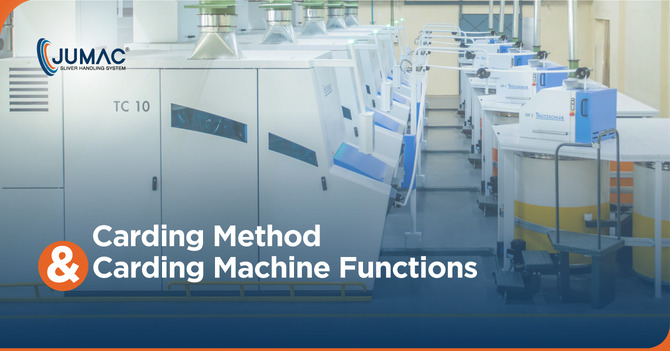
Carding Method and Carding Machine Functions
Often referred to as the ‘heart of the spinning process’, carding method is the second stage of spinning. In this stage, sliver – which, in essence, are the uniformly formed fibre strands – are obtained from the material fed into the carding machines. The carding stage is all about fibre individualisation from the cotton material coming in from the blowroom, followed by the formation of sliver from the carded cotton. The quality of the carding process directly influences the final yarn quality – and that’s exactly why spinning mills need to carefully select, set up and operate carding machine(s), as well use quality-assured spinning cans. Here is a detailed overview about all you need to know about the carding process, including the key function of carding machine:
What Exactly Is Carding Method?
Fibres received from the blow room generally have clumps and locks. The carding process in spinning mills helps in breaking up these blocks/clumps – so that the fibres are aligned in parallel positions with respect to each other. Different types of fibre blends and colours can be created through carding. Due care is taken to minimise the presence of moisture and friction – which can lead to increased sliver breakages. Expertly managed carding processes make sure that the yarn quality matches manufacturers’ expectations.
Preparing Cotton Fibres For Further Spinning Stages
There are multiple steps involved while getting cotton fibres (and woollen fibres, for that matter) ready for spinning. Carding and drawing are two of these phases. In particular, carding method is done to boost the processing efficiency levels, and render the best-quality yarns. In order to maximise the productivity of carded sliver, mills should always use advanced carding machines from OEMs like Trutzschler, Saurer, LMW, Rieter, and other such reliable brands. Quality-assured HDPE spinning cans, with high dimensional accuracy, are also required for efficient carding.
Also Read : Jumac Spinning Cans and OEM Machines Work Together to Improve Yarn Production
Broadly speaking, the carding stage in mills comprises several sub-steps. First, the ‘lapping’ procedure eliminates all dust and other impurities from the fibres. The fibres are loosened, as required, by the ‘willowing’ process. The main carding stage takes care of individualising the strands of fibre (which was tangled earlier). Finally, the drawing stage ensures further yarn quality improvements.
Carded Sliver and Combed Sliver
While carding is done for both combed and carded sliver, it is important to know about the differences between the two. In carded sliver production, the fibres go through two machines – with numerous teethed cards that ensure smooth fibre separation, removal of contaminants, and formation of sliver (by condensing the fibre strands). On the other hand, combed sliver is formed by passing the fibres through a machine with straight and metallic teeth. This ensures parallel placement of fibres in a line. Through combing, the evenness of the spun thread can be increased significantly.
Importance Of Carding In The Spinning Process
In addition to opening the tufts of cotton fibres and arranging them in the requisite pattern (parallel), the carding process eliminates all the neps that are generated in the mixing and the blowroom phases. The cotton web is systematically transformed into a uniform sliver by the carding machines. Extremely short fibres that are not suitable for yarn spinning are removed. Fibre blending is also another extremely important result of the carding process.
Ensuring optimal cleanliness of cotton lies at the very heart of quality yarn production. This is achieved during the carding phase. On average, the best carding machines can ensure upto 95% of fibre cleanness. Taken together, the cleanness achieved in the blowroom and carding stages can be 99% (provided all steps are carried out correctly). While it is practically impossible to get rid of ALL foreign material in the fibres, the percentage of such impurities in carded sliver can be as low as 0.04-0.05%.
Operators of carding machines in particular, and spinning mill operators in general, have to factor in the delicate nature of the sliver formed at this stage. The importance of smooth, careful material handling can hardly be overemphasised – and that, in turn, brings the need for using mechanically strong card cans, that have excellent stability and mobility, to the forefront. With the help of technology and innovation in textile industry, top spinning can manufacturers, like Jumac Cans, have a wide range of customised carding cans in their portfolio – that deliver great value for money.
Probable Problems In Carding Process
We have pretty much already established the benefits and purpose of carding. However, certain qualitative problems can crop up at times. These include the formation of neps, waste accumulation, and formation of holes in the card web patches. When the carding machines are not maintained and serviced on a regular basis, sliver variation can gradually increase. From time to time, it is also important to manually inspect the weight of sliver. This ensures that the final yarn is of the finest quality.
Note: Neps are the small fibre clumps/entanglements that cannot be unentangled. Unclean grid bars, improper stripping and high roller speeds are key factors behind the formation of neps in sliver.
The Role and Function of Carding Machines
From optimising the yarn quality to maximising spinning efficiency levels – perfect carding is essential for making the entire spinning process more seamless than ever. For nearly all types of fibres, the main function of carding machine remain relatively similar. Let us turn our attentions to these over here:
Once the fibre individualisation step is complete, the carding procedure handles the parallelisation requirements. Next, the neps that are present are disentangled (or discarded), and fibre impurities/foreign matter are removed. After the short fibres are eliminated as well, the fibre blending and orientation is done. Finally, the slivers are formed in the carding machine – and are moved on to the next stage, i.e., drawframing.
Given the importance of carding in the overall textile & yarn spinning process, it is only natural that leading OEMs are consistently coming up with advanced features in their carding machines. Spinning can suppliers also have different types of card cans in their portfolio – to meet the precise spinning requirements. It is important to ensure that the cans chosen are fully compatible with the card machines being used. Otherwise, mechanical glitches – leading to loss of productivity – becomes a very real risk.
Understanding The Carding Machinery Structure
Based on the application process in which they will be used, the structure of carding machines vary. In particular, there are differences in the physical attributes of jute carding and cotton carding machines. Also, while jute carding involves a single machine, there are two machines (beaker card and finisher card) in cotton carding.
Carding machines typically have a large number of different units. These include the chute feed (for feeding the fibre in the machine), the pipe ducts, the licker-in, the main cylinder, the stripping device, the flats, grid plates, transport & calendar rollers, & others.
The Final Word
In the carding stage, three processes – stripping, raising and carding – are done in combination. This, in turn, ensures that the material is processed uniformly in the machine, and risks of sliver deformities and other defects are removed.
Glitches in the carding stage can lead to a myriad of problems – right from sagging and/or patchy cotton webs and poor nep-elimination efficiency, to sliver breakage, increased U%, feed roller mapping, and more. These problems, in turn, affect the quality of the final output (studies have shown that nearly 90% of the cleaning efficiency is attributable to the carding phase). Mills need to make sure that the carding machinery is being operated optimally, and HDPE spinning cans are being used – for making the sliver handling process secure and seamless. In this context, it is also important to highlight the importance of sourcing the required card cans from reliable manufacturers (as well as using branded machinery). In the world of textile & yarn spinning, it is often said that “well carding is half spun” – and that sums up the importance of carding in the spinning process quite nicely.
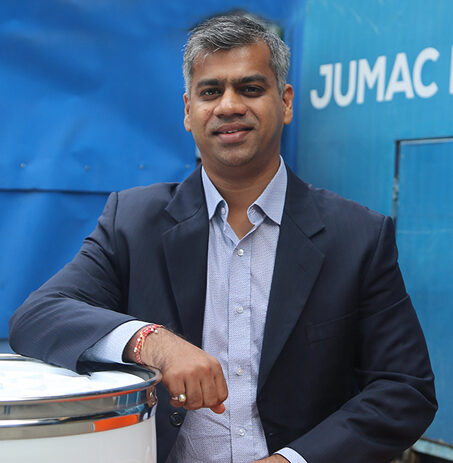
Passionate about transforming the industrial sector of textile and spinning industry with innovative solutions. Director at Jumac Manufacturing, leading spinning cans and accessories manufacturer and exporter from Kolkata, India.