In the overall yarn spinning process, the importance of sliver…
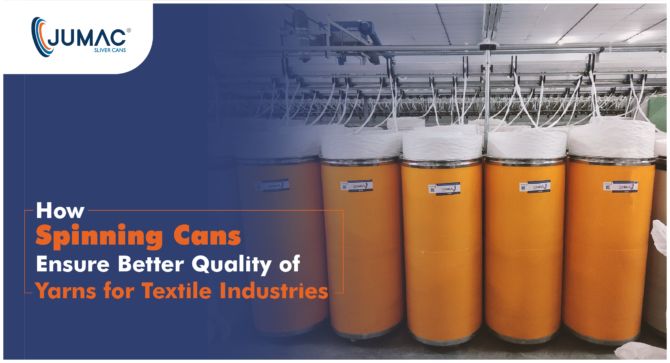
How Spinning Cans Ensure Better Quality of Yarns for Textile Industries
In recent years, the textile industry has witnessed continuous growth globally. Clothing and apparel companies are embracing synthetic fibres nowadays. Based on the globally rising per capita income and the persistent quantity of cotton available, synthetic yarn and blends will continue to grow to meet the increasing demands. Therefore, spinners are looking at upgrading their machinery to remain in the game. The spinners always aim to use the raw materials to produce high-quality yarn in an economically efficient manner. The main goal of any spinning mill is to maximize the profits and, on the other hand, to bring the yarn fully in line to attain elite garments. Increased efficiency can be achieved as an end result of making use of quality spinning cans in production. To obtain premium quality yarn and maximize productivity, retaining sliver properties is essential. Silver cans are used to hold the shape of the sliver firmly and reduce the sliver’s hairiness. Utilizing quality sliver cans is the first and most crucial step in the sliver handling system. Even small amounts of the flaw in the sliver have a massive impact on yarn characteristics. Sliver cans exporters clearly understand the customers’ needs and work closely with the spinning mills in crafting innovative designs of their cans models. Sliver cans manufacturers provide special after-sales packages to maintain the spinning cans to today’s needs.
Secure the quality of yarn with right sliver cans
Let’s ask spinning personnel how important the spinning cans are for textile mills. They will surely answer that this component significantly contributes to the production of a high-quality sliver. Spinning cans are used as a container to collect and store sliver. During various stages of the spinning process, sliver tends to break, resulting in hairiness and neps. A tiny imperfection in the sliver properties will affect the yarn quality enormously. Silver cans, along with their accessories, secure the yarn quality by retaining the original sliver parameters.
Compatibility
Spinning cans can be used for all yarn amounts and fibre types such as cotton, synthetic or blends. Sliver cans have a spring mechanism with different kinds of springs. Depending on the sliver type, it is combined and installed while handling the sliver so that the required criteria are optimally met. A simple, effective and user-friendly solution of adequately using the cans saves inventory and space in the textile mills. The tested and practically proven HDPE sliver cans and aluminium sliver cans are available for the rotor, ring and air-jet spinning machines. Silver cans manufacturers and exporters see that compatible spinning cans are created to adhere to diverse customer needs.
Competent sliver handling
The spinning cans ensure top quality in the sliver handling system. The high-grade silver can model been created so that sliver formation defects are consistently avoided, and the excellent sliver quality is retained. Textile industries rely on top quality yarn from the spinners to achieve elite garments. The spinning mills execute sliver coiling, storing and take-off most sensitively to maintain overall sliver regularity throughout the production process. The anti-static body of the sliver cans ensures zero fibre migration and thus minimizes the hairiness. Special springs such as box spring or pantograph spring assure practically frictionless movement of the cans without tilting. Spinning cans are therefore not just simple containers but an important quality criterion for spinning mills.
An essential requisite of spinning cans to ensure yarn quality
The body of the can should be robust and scratch-resistant but not heavy. Metal components of the cans must be precise and rust-free. The top and bottom plates/rims of the cans must be incorrect dimensional sizes and correct thickness to hold the shape of the cans. Galvanized steel or stainless steel with anti-corrosion properties is the preferred choice. When filling the spinning cans, the surface finish of the plate becomes important. The roughness is not important in the carded cans as here the plate exhibits a smooth surface. This is different from other subsequent spinning processes. On plates with smooth surfaces, the sliver starts to slip at the sliver coiling process’s initial stage. An excessively rough surface may damage the fibres, especially with the finer count of sliver. Based on these factors and years of experience, spinning cans manufacturers have created a plate with small rounded surface elevations as a good compromise.
A sliver draft changes the fineness of the sliver. For this reason, it is needed to select a spring with a tension suitable for the fibre weight and particularly with linear response during release and compression. It is also necessary for the spring to always be self-centred inside the can to avoid tilting of the plate that would cause liver damage. Adhesion free castor wheels are an especially important feature of the spinning cans, enhancing smooth transportation of sliver to subsequent machines in spinning mills. Sliver cans accessories improve the cans features, both in terms of work ergonomics and the yarn’s quality. If the spinning can have handles, the operator needs not hold the can by its rim. The sliver collected is therefore not touched by the operator and remains undamaged.
Furthermore, a special rubber band with an appropriate profile in different colours serves to protect the cans. It is also used to differentiate between the can contents. When it comes to machines and malfunctions, maintenance could help a business avoid downtime and improve quality, increase productivity, and save money. Any maintenance strategy plan aims to minimize downtime and keep production on schedule.
At present, sliver cans are available in various sizes and shapes with digitalization features to suit the current market trends. Customers’ flexibility that is a quick adaptation to market trends, is a key criterion for the sliver cans exporters to remain competitive today. Customers always appreciate the high productivity, consistent excellent yarn quality and low energy consumption. The main idea of spinning can creation is to collect and store different sliver types without any damage. The right choice of sliver cans enables the spinning mills to retain the silver properties ensuring better yarn quality. Indian silver cans exporters have carved a niche for themselves in the global market. They have established their leadership through profound knowledge and years of expertise.
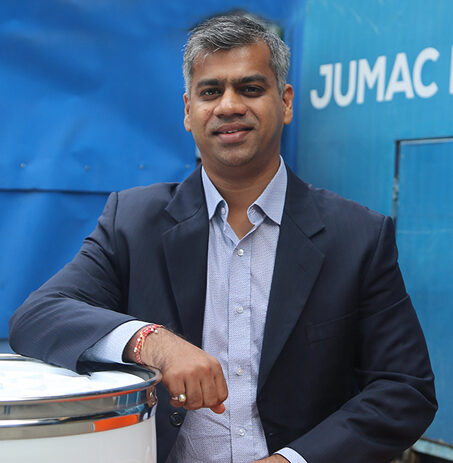
Passionate about transforming the industrial sector of textile and spinning industry with innovative solutions. Director at Jumac Manufacturing, leading spinning cans and accessories manufacturer and exporter from Kolkata, India.