The standard workflow of textile & yarn production is simple…
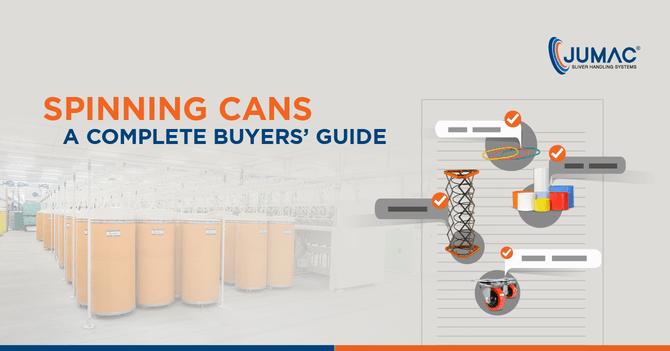
Spinning cans A Complete Buyers Guide
The role of quality-assured spinning cans in ensuring optimal yarn quality has already been well-documented. These cans find usage in various stages of spinning (carding, combing, roving, draw framing) – and when chosen carefully, they add value to the entire production chain at mills. And therein lies the challenge.
With all leading sliver can manufacturers in India constantly upgrading their portfolio to serve their customers, finding the ‘right’ set of spinning cans & accessories – that indeed bolstered operational efficiency and mill productivity levels – is often not the easiest task for buyers. To resolve this, we have come up with a detailed guide that will help mill-owners zero in on the best cans for spinning and get the best value from them.
The Can Size
To fit the category of can size requirement, it is essential to know the stage in which the can will be utilised. Spinning manufacturers offer several can sizes that store and collect slivers, at different stages of production. Cans, along with accessories, are available in small (225mm) to extra-large sizes (1200mm). In the textile industry, HDPE spinning cans of standard size and sturdy quality are preferred. Top manufacturers produce HDPE cans of customised sizes.
The Body Sheet
In spinning mills, parts of spinning cans are exposed to wear and tear. That is why shielding the cans’ external surface is essential to ensure durability and longevity. HDPE sheets provide another layer of cover guarding the can body from external impact and abrasion.
The sheets give the spinning cans more strength, and durability to their bodies. Made from high-density polyethene sheets (HDPE), sheets on the cans safeguard them from external physical wear and tear. Spinning mills prefer high-quality HDPE spinning cans, with a cylindrical body.
Body sheets should ideally be smooth, with an anti-static finish accompanied by a thick inner surface. It is also important to consider if the body sheet has enough butt weld tolerance and flexibility and is compatible with cylindrical can surfaces. Most spinning can accessory suppliers also promise to customise sheet colours as per the requirements.
The Machine Compatibility
Modern mills have accepted innovations in spinning technology with open arms. The spinning cans used in modern spinning mills must be compatible to be functional in the machinery. Cans with OEM compatibility are ideal to be used in several stages of the spinning process including carding, followed by combing, draw framing, roving, and finally, rotor spinning.
Ideally, spinning can manufacturers offer cans of sizes and requirements that fit all stages of spinning and transportation. For textile mills, HDPE spinning cans are best preferred, while for jute mills aluminium sliver cans are ideal.
The Can Covers (Top and Bottom)
During spinning, a lot of centrifugal force is exerted on the cans. This makes the cans prone to dislodging, tilting, and slipping from their bases – ultimately damaging the sliver quality in the process. Here is where the top and bottom covers of spinning cans come into play.
Bottom and top covers made from Acrylonitrile Butadiene Styrene (ABS) and Polypropylene copolymer (PPCP) are ideal for usage in spinning cans. An ideal top cover must have an anti-slippage body, superior surface grip, and added security to minimise sliver rupture.
The Top Rims & Bottom Bands
It is natural for cans in spinning mills to collide with each other while being stored or transported. However, that can hamper the sliver quality. Top rims and bottom band act as a safeguard against external collision of spinning cans. Stainless Steel (SS) or Galvanised Steel (GP) varieties of top rims are ideal for advanced spinning mills.
Combined with a smooth and seamless finish, top rims and bottom bands also cater to the sturdiness of the can body. A combination of contours offers a better grip to boost sliver handling across the mill floors. They also prevent rusting of the can edges.
The Springs
Sliver handling without springs being an essential component of sliver cans would be quite difficult. Thanks to this component, the bottom plates of cans remain in place and do not impact the quality of the sliver. It is essential to choose anti-rust, heat-treated, galvanised electro-welded springs for uniform loading and unloading of sliver which makes the process smoother in mills.
The Wheels
To facilitate transportation across the mill floor, the cans and trolleys need superior-quality wheels for smooth mill operations. Zinc-coated caster wheels with polypropylene and nylon are ideal in terms of performance, durability, and floor safety. Top manufacturers of spinning can accessories offer several caster wheel varieties– suitable for different stages of the spinning process. For optimised mill performance, caster wheels should ideally have ‘fluff-free’ technology, i.e., do not allow fibres to get stuck in the wheels.
The decision to buy spinning cans is not something that can be arrived at with haste. The onus is squarely on mill-owners and operators to understand their precise sliver handling requirements (e.g., number of cans needed for each stage, spring load suggestion, etc.), do their research to select a top, reputed spinning can manufacturer company, understand product specifications, and place orders accordingly. The quality and usability of spinning cans indeed make or break yarn quality and mill productivity – and as such, their selection has to be backed by adequate knowledge and research.
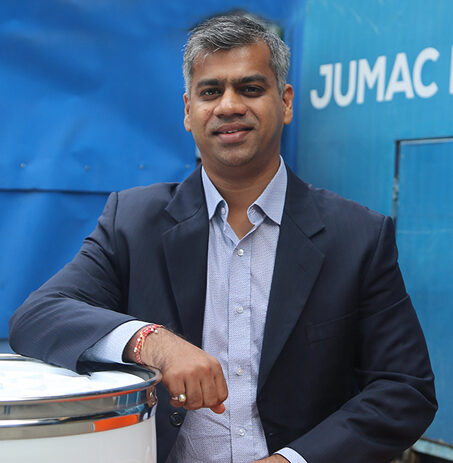
Passionate about transforming the industrial sector of textile and spinning industry with innovative solutions. Director at Jumac Manufacturing, leading spinning cans and accessories manufacturer and exporter from Kolkata, India.